Manufacturing Execution System
Providing a functional layer between enterprise resource planning (ERP) and process control systems, an MES gives decision-makers the data they need to make the plant floor more efficient and optimize production.
What is an Manufacturing Execution System ?
Follow MESA (Manufacturing Enterprise Solutions Association):
“A Manufacturing Execution System (MES) helps businesses ensure that their manufacturing operations and production output are working to maximum efficiency. It’s a software system that connects, monitors, and controls machines, work centers, and data flows on the factory floor. The MES does this by tracking and gathering real-time data throughout the production lifecycle and on every piece of equipment involved in the production process—from order to delivery.”
Top 5 benefits of MES
Manufacturing execution systems track a huge amount of data, producing real-time insights that can boost production efficiency and save costs. Other benefits of an MES include:
- Improved quality control: As quality control information is transmitted in real time, companies with an MES can immediately halt production as soon as issues are identified. This reduces waste, scrap, overages, and re-work.
- Increased uptime: An MES generates realistic production schedules by balancing personnel, material, and equipment resources. It integrates scheduling and maintenance to maximize product flow and asset utilization – increasing uptime and improving overall equipment effectiveness (OEE).
- Reduced inventory: A manufacturing execution system updates inventory records with new production, scrap, and non-conforming material so that your purchasing, shipping, and scheduling departments know exactly what material is on hand at all times. This reduces just-in-case inventory and work-in-progress (WIP) inventory – saving money on manufacturing, transportation, storage, and inventory monitoring.
- Paperless shop floor: Eliminating paperwork means there is less chance for human error. It also means that the data recorded from the shop floor is immediately available to decision-makers across all integrated systems, to inform real-time decision-making.
- Improved product tracking and genealogy: An MES follows the entire production cycle from beginning to end, grouping final parts or batches with the corresponding manufacturing data. This data allows for improved regulatory compliance for manufacturers that must conform to government or industry regulations.
Core MES Features
In 1997, the Manufacturing Enterprise Solutions Association International, or MESA, defined the 11 core manufacturing execution system functions. Although the MESA-11 model has evolved over time, those original 11 core functions provide the base to run almost any type of plant and are integral to today’s manufacturing execution systems. They are:
- Resource allocation and status: Use real-time data to track and analyze the status of resources, including machines, materials, and labor, to make allocation adjustments.
- Operations/detailed scheduling: Optimize performance by scheduling, timing, and sequencing activities based on priorities and resource capacity.
- Dispatching production units: Manage production data flow in real time to easily make quick, calculated adjustments in production dispatching.
- Document control: Manage and distribute documents – including work instructions, drawings, standard operating procedures, batch records, and more – so they’re accessible and editable.
- Data collection and acquisition: Track and collect real-time data about processes, materials, and operations and use it to make better decisions and increase efficiency.
- Labor management: Track worker schedules, qualifications, and authorizations to optimize labor management with less investment of time and resources from management.
- Quality management: Track quality deviations and exceptions for improved quality control management and documentation.
- Process management: Manage the entire production process from order release to finished goods. Gain insight into bottlenecks and points that affect quality while creating full production traceability.
- Maintenance management: Use data from your MES to identify potential equipment issues before they happen and adjust equipment, tool, and machine maintenance schedules to reduce downtime and increase efficiency.
- Product tracking and genealogy: Track the progress of your products and their genealogy for informed decision-making. Having the data of a product’s full history is extremely useful for manufacturers who must comply with government or industry regulations.
- Performance analysis: Compare results and goals to identify strengths and weaknesses in the overall process and use that data to make systems more efficient.
The evolution of MES standards
While the MESA-11 model focuses on core MES functions, the International Society of Automation (ISA) saw the need for consistent terminology and a consistent information model to define and integrate the activities between enterprise and control systems – so they developed the ISA-95 standard in the late ‘90s. By standardizing terminology, ISA-95 makes effective communication between stakeholders, such as suppliers and manufacturers, easier. And consistent models reduce the risk of error when integrating manufacturing sites with business systems.
ISA-95 defines the interface between control and enterprise functions to create levels of technology and business process. A simplified model of that hierarchy puts manufacturing execution systems at level three, between business planning and logistics and process control systems:
- Level 4 – ERP: Business planning and logistics
- Level 3 – MES: Manufacturing operations management
- Level 2 – Process control systems: Batch control
- Level 1 – Process control systems: Continuous control
- Level 0 – Process control systems: Discrete control
MES and ERP integration
In today’s manufacturing environment, it’s not a case of MES versus ERP; together MES and ERP bring operational clarity that neither system can provide on its own.
ERP focuses on creating and managing plant schedules including production, material use, delivery, and shipping – as well as gathering information about your business. Manufacturing execution systems, on the other hand, focus on managing and monitoring manufacturing operations and reporting on production line activities in real time.
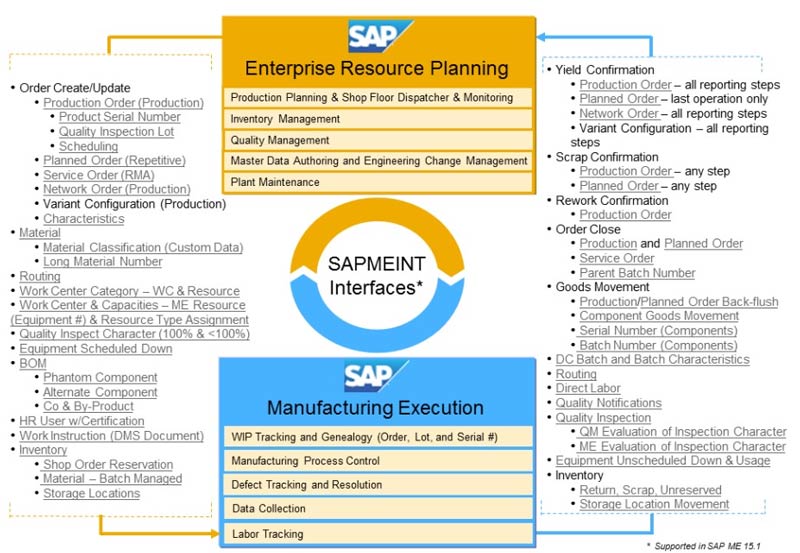
Together, an ERP and an MES create an integrated ecosystem, offering a holistic view of finance, procurement, supply chain management, manufacturing logistics, and more. Combining that information increases agility and provides robust data that improves forecasting on everything from sales to asset utilization to manufacturing management.
ERP systems give you the data to determine what products to manufacture, while an MES integrates ERP data with plant floor information to determine how to produce those products with less waste and more profit.
MES trends and new technologies
Fueled by advanced technologies, manufacturing execution systems are evolving to become service-oriented, modular, and connected.
Cloud connectivity is the backbone of smart factories, allowing advanced manufacturing systems, devices, products, and equipment to interact autonomously. IIoT (Industrial Internet of Things) devices and sensors across the supply chain are continually gathering and generating data. This real-time sharing of data helps smart factories to continually improve their operations – automating better workflows, customizing products and services, and growing smarter and more efficient over time.
MES software can also help manufacturers take advantage of a key trend in the evolution of manufacturing execution systems: customized production. Instead of mass production, your smart factory could move to mass personalization – and meet the demand for less expensive, highly tailored products with speed and affordability.
While personalization makes manufacturing more complex, advanced technologies can help manufacturing systems to react and pivot in real time. Artificial intelligence (AI) can improve production efficiency, handle predictive maintenance, and reduce waste. Tapping into machine learning capabilities, production lines can become increasingly smart and efficient. With virtual reality (VR), manufacturers can simulate processes and identify potential improvements. And they can integrate augmented reality (AR) solutions to reduce production downtime and optimize shop floor operations.
All of these advanced technologies and capabilities make it easier for companies to compete in a digital world – responding to demand rapidly and accurately with customized products that are lower in cost and higher in quality.
APZON IRS Vietnam provides a solution for MES system integrated with SAP Business One erp software system to create a comprehensive digital transformation platform for manufacturing businesses. More information about SAP Business One here.